Mastering About Aluminum Casting: Strategies Demystified
Mastering About Aluminum Casting: Strategies Demystified
Blog Article
Opening the Prospective of Aluminum Spreading: Proven Methods for Success
Light weight aluminum spreading has long been recognized for its convenience and extensive applications across numerous markets - about aluminum casting. However, uncovering the complete potential of this procedure requires even more than just standard understanding. By carrying out proven methods honed via years of industry experience and technology, producers can elevate their light weight aluminum casting operations to brand-new heights of performance and quality. From enhancing design factors to consider to streamlining manufacturing processes, the crucial lies in taking advantage of these strategies properly. Join us as we check out the important components that can push aluminum casting towards unparalleled success in today's open market landscape.
Benefits of Light Weight Aluminum Spreading
One of the primary benefits of light weight aluminum spreading is its light-weight nature, which contributes to fuel performance in sectors such as auto and aerospace. In addition, light weight aluminum is extremely malleable, permitting for detailed and complicated shapes to be easily generated with casting processes.
Moreover, light weight aluminum spreading supplies exceptional rust resistance, making it perfect for applications where exposure to harsh settings is a worry. The material likewise exhibits excellent thermal conductivity, which is helpful for industries calling for warm dissipation, such as electronics (about aluminum casting). Light weight aluminum is totally recyclable, aligning with the expanding emphasis on sustainable practices in contemporary production.
Style Factors To Consider for Casting
When taking into consideration casting layout, precise interest to information is critical to make certain the successful production of top notch parts. The layout stage plays a crucial duty in the total success of an aluminum spreading job. One key factor to consider is the option of proper geometries and attributes that assist in the spreading procedure. Designers have to take into consideration factors such as draft angles, fillets, and wall density to guarantee proper steel flow and solidification during casting.
Additionally, factors to consider connected to parting lines, gating systems, and risers are necessary to prevent defects like porosity and contraction. It is vital to enhance the style for efficient product usage and minimize post-processing requirements. Simulations and prototyping can be beneficial tools in reviewing and refining the spreading layout before major manufacturing.
Collaboration in between design engineers, manufacturers, and foundries is crucial to resolve any kind of potential difficulties early in the style stage. By incorporating these considerations into the spreading style process, manufacturers can boost product quality, decrease expenses, and eventually unlock the full potential of light weight aluminum casting.
Enhancing Casting Effectiveness
When aiming to boost casting performance in light weight aluminum casting tasks,Designing with an emphasis on enhancing product circulation and decreasing problems is necessary. To accomplish this, making use of simulation software application can help in determining prospective issues before the casting procedure starts. By imitating the circulation of molten aluminum, developers can change gating and riser styles to ensure appropriate filling and solidification, eventually minimizing the occurrence of like it defects such as porosity or contraction.
In addition, implementing proper heat treatment processes can improve the general casting performance. Warmth therapy can aid boost the mechanical homes of the light weight aluminum spreading, guaranteeing that the last element meets the needed specifications. Additionally, employing automation and robotics in the casting procedure can enhance manufacturing, decrease manual labor, and boost general efficiency.
Furthermore, constant monitoring and quality assurance during the casting procedure are important for determining any inconsistencies and making certain that the end products satisfy the preferred standards. By implementing these methods, makers can improve casting effectiveness, improve item high quality, and eventually attain greater success in aluminum casting projects.
High Quality Control in Aluminum Casting
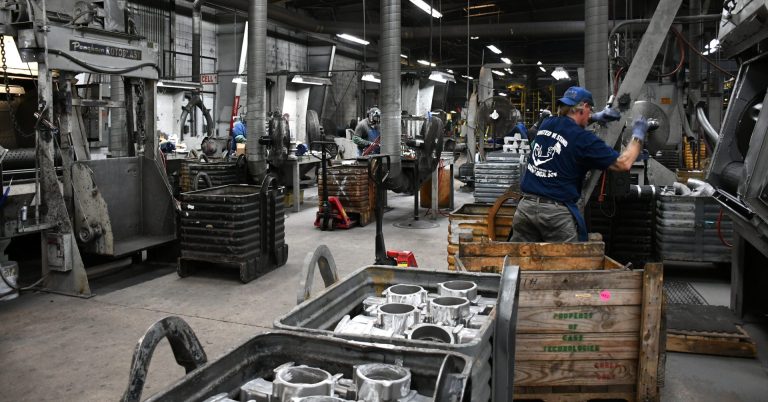
Reliable quality control methods play an essential role in making sure the accuracy and integrity of aluminum casting procedures. Quality control steps in aluminum casting incorporate an array of activities aimed at promoting details standards and determining deviations that might compromise the final item.
In addition to procedure control, quality assurance in aluminum spreading includes extensive screening and assessment treatments at various stages of production. Non-destructive screening approaches like ultrasonic testing and X-ray assessment help discover interior flaws without endangering the honesty of the cast parts. Aesthetic inspections, dimensional dimensions, and mechanical testing better make certain that the cast components fulfill the needed requirements and performance requirements. By executing durable quality assurance methods, light weight aluminum casting centers can deliver products that meet consumer expectations for quality, integrity, and efficiency.
Making The Most Of Success
To accomplish optimum financial efficiency, a comprehensive method for making the most of productivity within aluminum spreading procedures must be thoroughly designed and performed. One key facet of taking full advantage of productivity in aluminum spreading is maximizing manufacturing effectiveness.
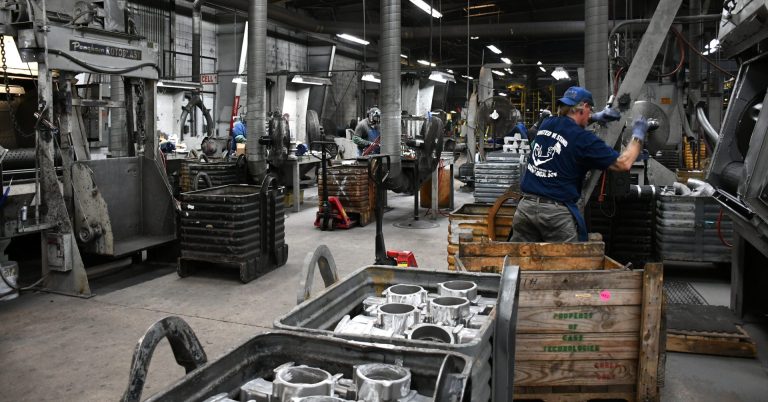
Furthermore, branching out item offerings and checking out brand-new markets can assist increase earnings streams. Comprehending customer requirements and market fads can lead strategic decisions to profit from arising possibilities. Buying r & d to innovate items or processes can likewise drive success through distinction and customer complete satisfaction.
Verdict
In final thought, light weight aluminum casting provides various benefits in terms of style toughness, versatility, and cost-effectiveness. By very carefully thinking about design considerations, enhancing casting performance, executing top quality control actions, and making the most of earnings, suppliers can open the complete capacity of aluminum casting. This see this site versatile and dependable procedure has shown to be an effective selection for a variety of industrial applications.
In addition, aluminum is highly malleable, allowing for elaborate and complex forms to be conveniently created through spreading procedures.Reliable high quality control practices play a critical duty in making certain the accuracy and integrity of light weight aluminum casting processes.In enhancement to procedure control, high quality control in aluminum casting entails rigorous screening and evaluation treatments at numerous stages of manufacturing. By executing robust top quality control techniques, light weight aluminum casting centers can deliver items that meet client assumptions for high quality, dependability, and performance.
By meticulously considering design factors to consider, improving casting effectiveness, applying quality control steps, and maximizing profitability, suppliers can unlock the complete capacity of light weight aluminum casting.
Report this page